News
Contact Us
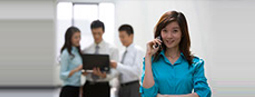
Suzhou Kaifa New Material Technology Co., Ltd.
Email:heqing@szkfxc.com
Email:sales@szbknm.com
Email:bkxc.bonnie@gmail.com
location:Home » News » Material properties
Production and application of boron nitride ceramics
edit:Kaifa Popularity:3335 Time:2020/3/25
Boron nitride is commonly known as white graphite. It has similar characteristics to graphite and is white in texture. There are two types of crystals: hexagonal and cubic, but usually a hexagonal structure. Under special conditions of high temperature and ultra high pressure, the hexagonal structure crystal form can be transformed into cubic crystal form. The powder is synthesized by the reaction of boron, boron halide or boric acid, borax, boron oxide and nitrogen-containing salts in a nitrogen or ammonia atmosphere. Boron nitride powder is white, light, loose, lubricating, easy to absorb moisture, etc., but does not work with acids, alkalis, glass and most metals, high mechanical strength, slightly higher than graphite, but no load at high temperature Softening phenomenon, can be used for mechanical turning, the accuracy can reach 1% mm. Boron nitride has a wide range of uses, and its powder can be used as an excellent lubricant and mold release agent, while ceramics can be used as crucibles, boats, liquid metal conveying pipes, rocket nozzles, high-power device bases, and semiconductor components for melting evaporated metals Miscellaneous sources, and various high-temperature (high-voltage, high-frequency) insulation and cooling components. Cubic boron nitride is a superhard material similar to diamond.
I. Methods for synthesizing boron nitride powder There are more than ten methods for synthesizing boron nitride powder, but there are mainly three methods that can realize industrial production.
1. Borax-ammonium nitride method. In this method, borax is first dehydrated in a vacuum at 200-400 ° C, ammonium nitride is introduced to dissolve into a saturated solution, and then impurities are removed by filtration, and the result can be repeated.Then the above raw materials are crushed and dried, mixed with borax and ammonium chloride at a ratio of 7: 3 (weight ratio), pressed into a compact, and synthesized in a reaction furnace. The reaction temperature is 900-1000 ° C, and the temperature is maintained for 6 hours. NH3 was introduced during the reaction to make up for the lack of nitrogen when the reactants themselves formed. The main reaction formula is: Na2B4O7 + 2NH4Cl + 2NH3 → 4BN + 2NaCl + 7H2O. The reaction product is immersed in water to remove the remaining boric acid, sodium chloride and other impurities, and dried and pulverized to obtain boron nitride powder with a purity of up to 97%.
2. Borax one urea method. Borax is dehydrated, dried, and pulverized, and urea is purified, dried, and pulverized. Borax and urea should be uniformly mixed according to the ratio of 1: 15-2, and then placed in a quartz glass, corundum, graphite or stainless steel container, and placed in a reaction furnace. When the temperature is raised to 100 ° C, it is held for 30 minutes and at 140 ° C. 2. Incubate at 180 ℃ for 2 hours, at 800 ℃ for 2 hours, at the final temperature of 800-1000 ℃ for 2-4 hours, when the temperature is below 300 ℃, first introduce nitrogen, and change it at 300 ℃ or above. Pass in ammonia gas. The main chemical reactions are: Na2B4O7 + 2CO (NH2) 2 → 4BN + Na2O + 4H2O + 2CO2 ↑ The product produced by the reaction is acid-washed with hydrochloric acid, Na2O is removed therefrom, then Cl- ion is washed with water, and H3BO3 is washed with alcohol. After repeated treatment with water and alcohol, drying was performed to obtain boron nitride powder (containing 95% BN).
3. Boron method. Boronium is used as the main raw material, and tricalcium phosphate is used as the filler. The mixing ratio of the two is 5: 3. Dry mixing, adding water to form a paste, granulation, and drying below 80 ° C. The mixture is put into a quartz tube or a corundum tube electric furnace for nitriding reaction. The furnace body should be tilted slightly to facilitate drainage. The reaction temperature is 900-1000 ° C, the temperature is maintained for 6 hours, and NH3 gas is introduced. The main reaction formula is: B2O3 + 2NH3 → 2BN + 3H2O The reaction product is washed with 3% hydrochloric acid for 16 hours to remove Ca3 (PO4) 2 and H3BO3, and then washed with 25% hydrochloric acid for 3 hours, and then washed with HCl. It is dried below 180 ° C, washed with alcohol to remove H3BO3, and finally dried to obtain BN.
2. Manufacturing of boron nitride products The methods of manufacturing boron nitride products include cold pressing sintering and hot pressing sintering. Here is the hot-pressing sintering method. First, mix fine boron nitride powder with a particle size of less than 5 microns and a small amount of additives, pre-press once in an isostatic press at a pressure of 100-150 MPa, and then crush it into a material smaller than 0.5 mm and load it into a graphite mold Medium, heated and pressurized in a hot-pressed furnace heated by carbon tubes, the highest temperature is 1600-1900 ℃, the pressure is 20-25MPa, the temperature is kept for several minutes to one hour, and it is ready for machining after cooling. At this time, it should be pointed out that the presence or absence of B2O3 in the material has a great impact on the performance of the product. When B2O3 is not present, the product is difficult to obtain high density, but the water resistance is good. When B2O3 is present, the product is easy to densify, but the stability to water is poor. Therefore, for pure boron nitride materials that do not contain B2O3 (difficult to heat sintering), an appropriate amount of binding agent, such as B2O3, boron phosphate or CaO-B2O3-Al2O3, etc. should be added to promote sintering without affecting the stability of the product; and For boron nitride powders with high B2O3 content, appropriate stabilizers such as Al, AlN, CaO-Al2O3, SiO2, etc .; or for boron nitride products containing B2O3 after hot pressing, under vacuum or argon, nitrogen High temperature treatment in the atmosphere will make B2O3 volatilize. Effect of additives on sinterability and stability of BN. See table.
of boron nitride products Boron nitride products made by hot pressing method, the highest temperature in N2 or Ar atmosphere is up to 2800 ℃, without obvious melting point, sublimation at 3000 ℃ in 0.1MPaN2. However, the stability is poor in an oxidizing atmosphere, and the use temperature is only below 900 ° C. Boron nitride products have low expansion coefficient, high thermal conductivity, excellent thermal shock stability, and are good insulators. Boron nitride also has many special properties. It can be used as a high temperature thermocouple protection tube, a vessel for smelting metal, and a thermal shielding material in space navigation only in the use of refractory materials. In short, boron nitride products show broad prospects for future high-tech product development.
======================================================= ======================================================= ================
Oily Nano Boron Nitride Ceramic Lubricant Additive
Oily Nano Boron Nitride Ceramic Lubricant Additive directly forms a ceramic on the metal surface through a chemical coupling reaction during mechanical operation. The metal interface ceramizes all friction surfaces, realizing the universal application of ceramic metal materials in traditional industries.
All the current lubricating oils or lubricating oil additives are for the treatment of lubricating oils. Some nanotechnology lubricant additives are ultra-fine powders processed to nano-level powders, which are extremely small, and fill tiny voids on the metal surface to reduce friction and reduce wear. Oily nanometer boron nitride ceramic lubricating oil additive is a technology to change the material, while lubricating oil or grease is only the appearance of the form, the main mechanism is chemical coupling.Chemical coupling is the formation of chemical bonds. It was first applied to glass fiber reinforced plastics. The application of ceramic-metal coupling technology in the field of lubrication is the world‘s first. Ceramic lubricating technology consists of a ceramic chemical coupling agent that forms a chemically bonded ceramic structure on the metal surface through frictional heat during the operation of the tool. Ceramic lubrication technology is to form chemical bonding with metals (** cal Bonding), which fundamentally changes the properties of metal surfaces and changes metal materials into ceramic materials.
Because the machine tool forms a ceramic metal material, the machine and product have achieved amazing results because of the characteristics of the ceramic metal material. It is incomparable with any other technology and product, and cannot be achieved by any other product in the world. It has derived boron nitride ceramic metal super lubricating products, as well as other additional products, such as: ceramic bearings, ceramic gearboxes , ceramic engines, ceramic tools, and so on.
1) Ceramicized bearings: Bearings with a designed life of 100 hours can be operated for thousands of hours with ceramic lubrication technology, and can even reach more than 4500 hours.
2) Ceramicized gearbox: The parts of the gearbox often cause damage when the lubricant is not available.
Ceramic lubrication technology allows the gearbox to function normally without oil.
3), ceramic engine: automobile engine, improve exhaust emissions, enhance power, etc.
4). Saving non-renewable energy and resources:
saving automobile fuel, an average of 5%, saving petroleum energy.
5) Environmental protection:
Reduce CO, HC, NOx. Especially reducing NOx is the most difficult problem in the world. The boron nitride ceramic metal lubrication test data shows that the reduction of nitrogen oxides can reach 78-80%.
In addition, boron nitride ceramic lubricants also effectively reduce work noise, which is also a problem to be solved by engines, bearings and various mechanical equipment.
Product features: Does not contain any solid particles, and is well dispersed in the lubricant for a long time, which can improve the anti-backpressure performance of the lubricant, reduce the coefficient of friction, and form a boron nitride ceramic protective layer on the friction surface.
I. Methods for synthesizing boron nitride powder There are more than ten methods for synthesizing boron nitride powder, but there are mainly three methods that can realize industrial production.
1. Borax-ammonium nitride method. In this method, borax is first dehydrated in a vacuum at 200-400 ° C, ammonium nitride is introduced to dissolve into a saturated solution, and then impurities are removed by filtration, and the result can be repeated.Then the above raw materials are crushed and dried, mixed with borax and ammonium chloride at a ratio of 7: 3 (weight ratio), pressed into a compact, and synthesized in a reaction furnace. The reaction temperature is 900-1000 ° C, and the temperature is maintained for 6 hours. NH3 was introduced during the reaction to make up for the lack of nitrogen when the reactants themselves formed. The main reaction formula is: Na2B4O7 + 2NH4Cl + 2NH3 → 4BN + 2NaCl + 7H2O. The reaction product is immersed in water to remove the remaining boric acid, sodium chloride and other impurities, and dried and pulverized to obtain boron nitride powder with a purity of up to 97%.
2. Borax one urea method. Borax is dehydrated, dried, and pulverized, and urea is purified, dried, and pulverized. Borax and urea should be uniformly mixed according to the ratio of 1: 15-2, and then placed in a quartz glass, corundum, graphite or stainless steel container, and placed in a reaction furnace. When the temperature is raised to 100 ° C, it is held for 30 minutes and at 140 ° C. 2. Incubate at 180 ℃ for 2 hours, at 800 ℃ for 2 hours, at the final temperature of 800-1000 ℃ for 2-4 hours, when the temperature is below 300 ℃, first introduce nitrogen, and change it at 300 ℃ or above. Pass in ammonia gas. The main chemical reactions are: Na2B4O7 + 2CO (NH2) 2 → 4BN + Na2O + 4H2O + 2CO2 ↑ The product produced by the reaction is acid-washed with hydrochloric acid, Na2O is removed therefrom, then Cl- ion is washed with water, and H3BO3 is washed with alcohol. After repeated treatment with water and alcohol, drying was performed to obtain boron nitride powder (containing 95% BN).
3. Boron method. Boronium is used as the main raw material, and tricalcium phosphate is used as the filler. The mixing ratio of the two is 5: 3. Dry mixing, adding water to form a paste, granulation, and drying below 80 ° C. The mixture is put into a quartz tube or a corundum tube electric furnace for nitriding reaction. The furnace body should be tilted slightly to facilitate drainage. The reaction temperature is 900-1000 ° C, the temperature is maintained for 6 hours, and NH3 gas is introduced. The main reaction formula is: B2O3 + 2NH3 → 2BN + 3H2O The reaction product is washed with 3% hydrochloric acid for 16 hours to remove Ca3 (PO4) 2 and H3BO3, and then washed with 25% hydrochloric acid for 3 hours, and then washed with HCl. It is dried below 180 ° C, washed with alcohol to remove H3BO3, and finally dried to obtain BN.
2. Manufacturing of boron nitride products The methods of manufacturing boron nitride products include cold pressing sintering and hot pressing sintering. Here is the hot-pressing sintering method. First, mix fine boron nitride powder with a particle size of less than 5 microns and a small amount of additives, pre-press once in an isostatic press at a pressure of 100-150 MPa, and then crush it into a material smaller than 0.5 mm and load it into a graphite mold Medium, heated and pressurized in a hot-pressed furnace heated by carbon tubes, the highest temperature is 1600-1900 ℃, the pressure is 20-25MPa, the temperature is kept for several minutes to one hour, and it is ready for machining after cooling. At this time, it should be pointed out that the presence or absence of B2O3 in the material has a great impact on the performance of the product. When B2O3 is not present, the product is difficult to obtain high density, but the water resistance is good. When B2O3 is present, the product is easy to densify, but the stability to water is poor. Therefore, for pure boron nitride materials that do not contain B2O3 (difficult to heat sintering), an appropriate amount of binding agent, such as B2O3, boron phosphate or CaO-B2O3-Al2O3, etc. should be added to promote sintering without affecting the stability of the product; and For boron nitride powders with high B2O3 content, appropriate stabilizers such as Al, AlN, CaO-Al2O3, SiO2, etc .; or for boron nitride products containing B2O3 after hot pressing, under vacuum or argon, nitrogen High temperature treatment in the atmosphere will make B2O3 volatilize. Effect of additives on sinterability and stability of BN. See table.
Effect of Table Additives on Sinterability and Stability of BN
BN + Additive |
Bulk density g / cm3 |
Weight loss after 800CH2O treatment,% |
||
10 hours |
20 hours |
30 hours |
||
BN with 14% B2O3 |
2.10 |
|||
BN + 1% Al |
2.12 |
0.96 |
1.42 |
1.80 |
BN + 5% Al |
2.04 |
0 |
0 |
0 |
BN + 5% AlN |
2.16 |
0.32 |
0.50 |
0.60 |
BN + 5% CaO, |
2.17 |
0.31 |
0.38 |
0.44 |
Pure BN |
1.22 |
0 |
||
Pure BN + 5% B2O3 |
2.07 |
3.15 |
||
Pure BN + 10% B2O3 |
2.08 |
5.79 |
||
Pure BN + 10% 2CaO · 9B2O3 |
2.01 |
0.33 |
||
Al2O3 |
||||
Pure BN + 10% BPO4 |
2.07 |
6.20 |
of boron nitride products Boron nitride products made by hot pressing method, the highest temperature in N2 or Ar atmosphere is up to 2800 ℃, without obvious melting point, sublimation at 3000 ℃ in 0.1MPaN2. However, the stability is poor in an oxidizing atmosphere, and the use temperature is only below 900 ° C. Boron nitride products have low expansion coefficient, high thermal conductivity, excellent thermal shock stability, and are good insulators. Boron nitride also has many special properties. It can be used as a high temperature thermocouple protection tube, a vessel for smelting metal, and a thermal shielding material in space navigation only in the use of refractory materials. In short, boron nitride products show broad prospects for future high-tech product development.
======================================================= ======================================================= ================
Oily Nano Boron Nitride Ceramic Lubricant Additive
Oily Nano Boron Nitride Ceramic Lubricant Additive directly forms a ceramic on the metal surface through a chemical coupling reaction during mechanical operation. The metal interface ceramizes all friction surfaces, realizing the universal application of ceramic metal materials in traditional industries.
All the current lubricating oils or lubricating oil additives are for the treatment of lubricating oils. Some nanotechnology lubricant additives are ultra-fine powders processed to nano-level powders, which are extremely small, and fill tiny voids on the metal surface to reduce friction and reduce wear. Oily nanometer boron nitride ceramic lubricating oil additive is a technology to change the material, while lubricating oil or grease is only the appearance of the form, the main mechanism is chemical coupling.Chemical coupling is the formation of chemical bonds. It was first applied to glass fiber reinforced plastics. The application of ceramic-metal coupling technology in the field of lubrication is the world‘s first. Ceramic lubricating technology consists of a ceramic chemical coupling agent that forms a chemically bonded ceramic structure on the metal surface through frictional heat during the operation of the tool. Ceramic lubrication technology is to form chemical bonding with metals (** cal Bonding), which fundamentally changes the properties of metal surfaces and changes metal materials into ceramic materials.
Because the machine tool forms a ceramic metal material, the machine and product have achieved amazing results because of the characteristics of the ceramic metal material. It is incomparable with any other technology and product, and cannot be achieved by any other product in the world. It has derived boron nitride ceramic metal super lubricating products, as well as other additional products, such as: ceramic bearings, ceramic gearboxes , ceramic engines, ceramic tools, and so on.
1) Ceramicized bearings: Bearings with a designed life of 100 hours can be operated for thousands of hours with ceramic lubrication technology, and can even reach more than 4500 hours.
2) Ceramicized gearbox: The parts of the gearbox often cause damage when the lubricant is not available.
Ceramic lubrication technology allows the gearbox to function normally without oil.
3), ceramic engine: automobile engine, improve exhaust emissions, enhance power, etc.
4). Saving non-renewable energy and resources:
saving automobile fuel, an average of 5%, saving petroleum energy.
5) Environmental protection:
Reduce CO, HC, NOx. Especially reducing NOx is the most difficult problem in the world. The boron nitride ceramic metal lubrication test data shows that the reduction of nitrogen oxides can reach 78-80%.
In addition, boron nitride ceramic lubricants also effectively reduce work noise, which is also a problem to be solved by engines, bearings and various mechanical equipment.
Product features: Does not contain any solid particles, and is well dispersed in the lubricant for a long time, which can improve the anti-backpressure performance of the lubricant, reduce the coefficient of friction, and form a boron nitride ceramic protective layer on the friction surface.
Next:
Application of z...
Previous:
Hyflux ceramics ...