News
Contact Us
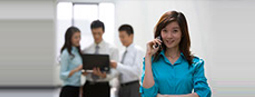
Suzhou Kaifa New Material Technology Co., Ltd.
Email:heqing@szkfxc.com
Email:sales@szbknm.com
Email:bkxc.bonnie@gmail.com
location:Home » News » Material properties
The main application of zirconia
edit:Kaifa Popularity:2381 Time:2020/3/25
The main applications of fused zirconia are as follows:
1.Refractory and casting
Zirconia has two major refractory markets. The first is continuous cast steel refractories, especially isobaric products. These products include outlets and immersion nozzles for intermediate channels and ladles. Sliding baffles also use zirconia, especially for central areas exposed to the highest temperatures. Both partially stabilized calcium oxide and magnesium oxide zirconium dioxide are used, however, calcium oxide is generally cheaper.
The second major market is the production of fused alumina-zirconia-silica (AZS) refractories for the glass industry. Zirconia provides high temperature and corrosion resistance to molten glass. Since no reaction zone occurs, no crushed stone is generated in the glass.
These products are mainly made of molten monoclinic zirconia (or zirconia) containing alumina and silica in an electric arc furnace. The melt flow is then poured into sand or sometimes mechanically designed blocks made of graphite.
Aluminum zirconium silicon (AZS) refractories are classified by zirconia content. This classification limits the product‘s corrosion resistance. Generally, the industry produces 33% zircon, 37% zircon and 41% zircon products. Sometimes zircon sand with monoclinic zirconia is also added to the furnace in order to adjust the zirconia content.
2. Investment casting
For zirconia, this is another major niche market. Special product castings, such as aerospace engines, use zirconia as a coating for models. Products included here include turbine-driven paddles and golf clubs. Zircon is used in investment casting because it can form actual contact with hot metal alloys to protect the mold from thermal shock.
3.Dyes and pigments
In the ceramics industry, the production of sanitary ceramics, tableware, floor tiles and wall tiles all require colored glazes, which can withstand high-temperature baking. Zirconia is used to prepare pigments such as ochre yellow, vanadium blue, and iron coral powder. Cubic zircon is also used to make ceramic pigments. The metallic pigment is added to the monoclinic zirconia or zirconia and the mixture, and then milled and fired. After washing with water, the product was ground again to a fine powder. This product is added to a ceramic glaze with some alumina and feldspar, mainly silica powder. Most ceramic pigment production has shifted to Asia, with limited production in the United States and Europe.
4.Grinding material
Zirconium oxide and alumina are mixed to make coarse abrasive particles. The combination of abrasive wheels and coated abrasives are used to polish steel and metal alloys.
5. Advanced ceramics and special products
For stabilized zirconia, electronic component firing regulators are a major market. Stabilized zirconia is also used in oxygen sensors and fuel cell separators because of its unique ability to allow oxygen ions to move freely in the crystal structure under high temperature conditions. This high degree of ionic conductivity (and low-variation electron conductivity) makes it one of the most useful electrical ceramic materials. Chemical-grade zirconia often has more applications than fused products on these markets. Other specialty markets include suction pumps and high-value components, special tool parts, and brake pad linings. The gem market also uses yttria-stabilized zirconia with a fully stabilized cubic phase, which is a cheaper alternative to the diamond industry in the jewelry industry.
Next:
Silicon nitride ...
Previous:
Application of z...