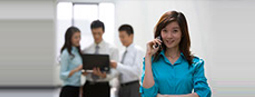
Suzhou Kaifa New Material Technology Co., Ltd.
Email:heqing@szkfxc.com
Email:sales@szbknm.com
Email:bkxc.bonnie@gmail.com
Brief introduction of 10 kinds of sintering process of alumina ceramics
1. Atmospheric pressure sintering
Atmospheric pressure sintering means that the material is sintered at atmospheric pressure without being pressurized, and it is currently the most commonly used sintering method. It includes normal pressure sintering under air conditions and normal pressure sintering under certain gas atmosphere conditions. This method has a higher sintering temperature, higher requirements on the furnace, and a greater waste of energy.
Al 2 O 3 has a high melting point, so the preparation of Al 2 O 3 ceramics often requires the addition of sintering aids, which are dense by liquid phase sintering. This method can be generally promote of Al 2 O . 3 sintered ceramics, of Al 2 O . 3 ceramics by liquid phase sintering, a liquid phase chemical reaction, and promote the diffusion of viscous flow to reach the mass transfer process and the rearrangement of particles, decrease of Al 2 O 3 Ceramic sintering temperature, accelerate effective sintering.
Since there is no external driving force for atmospheric pressure sintering, it is very difficult to exclude all the pores inside the ceramic to reach the theoretical density. The special sintering process refers to the addition of sintering driving force during the sintering process of alumina ceramics to promote the densification of the ceramics. At present, the common special sintering processes mainly include hot pressing sintering, hot isostatic pressing sintering, microwave heating sintering, microwave plasma sintering, discharge plasma sintering, etc.
2. Hot pressing sintering
Hot pressing sintering is to apply unidirectional pressure to the sample at high temperature to promote the ceramic to achieve full density. Compared with conventional sintering, sintering at a pressure of 15 MPa reduces the sintering temperature of ceramics by 200°C and increases the density by 2%, and this trend increases with increasing pressure. For pure alumina ceramics, conventional sintering requires a temperature above 1800°C; hot-press sintering at 20 MPa only requires 1500°C.
The pressure provided by hot pressing sintering promotes the flow of atoms in the particles, and the pressure and surface energy together act as a driving force to enhance the diffusion effect. Since hot pressing sintering can sinter at a lower temperature, the growth of crystal grains is suppressed, and the obtained sample is dense and uniform, with small crystal grains and high strength. However, it is not suitable to produce products that are too high, too thick, and complex in shape. The production scale is small and the cost is high.
3. Hot isostatic sintering
Hot isostatic sintering is sintering that applies pressure to all directions of the ceramic body at the same time, reduces the sintering temperature of the ceramic, and at the same time, the ceramic structure obtained by sintering is uniform and has good performance. Although hot isostatic sintering can successfully reduce the sintering temperature of ceramics and obtain complex shapes, hot isostatic sintering needs to encapsulate or pre-sinter the green body in advance, and the pressure conditions will be more severe.
4. Ultra-high pressure sintering
Ultra-high pressure sintering means sintering under higher pressure conditions. Due to the higher pressure, atom diffusion is suppressed and the nucleation barrier is relatively small. Therefore, high density (>98%) can be obtained at lower temperature Purity alumina ceramics. In the ultra-high pressure sintering process, the existence of pressure increases the vacancy and atom diffusion rate in the particles, and the pressure and surface energy together serve as the driving force for sintering, which increases the diffusion effect. Ultra-high pressure sintering usually only needs to be carried out at a relatively low temperature, which suppresses the abnormal growth of grains, thereby obtaining high-purity alumina ceramics with high densification, fine grain size and uniform distribution.
5. Sintering by microwave heating
Microwave heating sintering utilizes the interaction between microwaves and ceramics, because the dielectric effect causes both the inside and the surface of the ceramic to be sintered simultaneously. Microwave sintering is different from other sintering methods. Its hot gas flow is from inside to outside, which is conducive to the diffusion of the gas inside the body. At the same time, microwave makes the activity of the crystal grains increase and it is easier to migrate to promote densification.
Compared with other sintering methods, microwave sintering can quickly heat up and sinter, the temperature field is uniform, the thermal stress is small, and there is no pollution. The sintering temperature of microwave sintering is 100℃ to 150℃ lower than conventional sintering, and the sintering time is nearly an order of magnitude shorter than conventional sintering. Under the same conditions, the density of microwave sintering is obviously higher than that of conventional sintering. Microwave sintering can sinter objects with complex shapes, and the sintered ceramic has small internal crystal grains, good uniformity and good fracture toughness.
6. Microwave plasma sintering
Compared with conventional sintering, microwave plasma sintering can reduce the sintering temperature by 200℃ under the same conditions, and has a fast sintering speed, small grain size and high mechanical strength. One reason why microwave plasma sintering promotes densification is rapid temperature rise. Rapid temperature rise reduces the growth of grains caused by surface diffusion and provides a strong driving force and a short distance for volume diffusion and grain boundary diffusion. Lower the sintering temperature of alumina ceramics and refine the grains.
7. Spark plasma sintering
Spark plasma sintering is a newer sintering method developed in recent years. It uses the instantaneous high temperature field generated by pulse energy and pulse pressure to realize the spontaneous heating of the internal crystal grains of the ceramic to activate the crystal grains. The method has the advantages of rapid temperature rise, rapid temperature decrease and short heat preservation time, which inhibits the growth of crystal grains, shortens the preparation period of ceramics, and saves energy. Spark plasma sintering is actually a new hot-press sintering method. The obtained ceramic samples have uniform grains, high density, and good mechanical properties. It is a valuable and promising sintering method.
In the process of preparing high-purity alumina ceramics by spark plasma sintering, the heating rate has a greater influence on the densification of samples at different stages of sintering. In the initial stage of sintering, a faster heating rate can increase the density of the sintered body, while in the later stage of sintering, the faster heating rate will cause the density of the sintered body to decrease.
8. Two-step sintering method
The two-step sintering method heats the sample to a specific temperature (T1) to eliminate the subcritical pores in the green body, and then lowers it to a lower temperature (T2) to make the green body dense. In the low-temperature sintering stage in the two-step sintering process, since the grain boundary migration is higher than the activation energy required for grain boundary diffusion, the grain boundary diffusion is mainly used in this stage. Therefore, in the second stage of the two-step sintering process, the green body is continuously densified, but the grains will not grow too fast. In the low-temperature sintering stage of the two-step sintering method, the prerequisite for the complete compaction of the green body is that during the shrinkage of the green body, the pores in the green body gradually become closed pores.
9. Microwave two-step sintering
The two-step sintering can be carried out on a traditional sintering furnace, the equipment cost is low, and it has strong application value. However, the two-step sintering is a relatively slow sintering process because it needs to be kept at the second temperature for a long time. Microwave heating usually has the advantages of integral heating and rapid heating, and few studies have combined microwave heating with two-step heating. However, the characteristics of microwave heating can reduce the sintering temperature and shorten the sintering time, which will help further refine the grains and effectively shorten the production cycle of the two-step method.
10. High vacuum sintering
High vacuum sintering is a sintering technique for sintering ceramic blanks under high vacuum. Vacuum sintering has attracted the attention of many scholars in the preparation of ceramics with low porosity and small size due to the advantages of reducing the heating rate, inhibiting abnormal grain growth and reducing irregular porosity.
High vacuum sintering can not only increase some properties of high-purity alumina ceramics, but also reduce impurities at the grain boundaries and pores in the sintered body. In the process of preparing high-purity alumina ceramics by vacuum sintering, oxygen ions in the alumina lattice are easily lost, forming a large number of oxygen ion vacancies, and the concentration of aluminum ions is relatively increased, which leads to the acceleration of the aluminum ion diffusion process, which is beneficial to the sintering process.
Attachment: Performance comparison of alumina ceramics prepared by different sintering methods
Source: Dai Jinshan. Atmospheric pressure of high-purity alumina ceramics
And hot press sintering and performance research
Reference Material: Powder Net
This information originates from the Internet for academic exchange only. If infringement please contact us to delete immediately