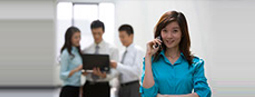
Suzhou Kaifa New Material Technology Co., Ltd.
Email:heqing@szkfxc.com
Email:sales@szbknm.com
Email:bkxc.bonnie@gmail.com
Main properties of advanced ceramic alumina ceramic substrates
Advanced ceramic materials, also known as precision ceramic materials, refer to products with excellent performance produced by using refined high-purity and ultra-fine inorganic compounds as raw materials and advanced preparation technology. According to the requirements of engineering technology for product performance, the manufactured products can be piezoelectric, ferroelectric, conductive, semiconductor, magnetic, etc. or have high strength, high toughness, high hardness, wear resistance, corrosion resistance, high temperature resistance, high thermal conductivity, Excellent properties such as thermal insulation or good biocompatibility.
Alumina (Al2O3) ceramics have good comprehensive properties and are currently the most mature. Alumina (Al2O3) ceramics are rich in raw materials, low in price, high in strength, hardness, thermal shock resistance, insulation, chemical stability, and good adhesion to metals. At present, Al2O3 is the main material of ceramic substrates. According to the Shanghai Institute of Silicate Research, Chinese Academy of Sciences, the Rockwell hardness of alumina (Al2O3) ceramics is HRA80-90, second only to diamond and far exceeding the wear resistance of wear-resistant steel and stainless steel. As determined by the Institute of Powder Metallurgy of Central South University, the wear resistance of alumina (Al2O3) ceramics is 266 times that of manganese steel and 171.5 times that of high-chromium cast iron. The density of alumina (Al2O3) ceramics is 3.5g/cm3, which is only half of that of steel, which can greatly reduce the load of equipment.
According to a study by Insight Partners on “European Alumina Ceramics Market Forecast to 2027 – Impact and Analysis of COVID-19 – By Application (Electronics & Semiconductors, Energy & Power, Military & Defense, Automotive, Industrial, Medical, etc.), "The alumina ceramics market is expected to grow from USD 9,117.4 million in 2019 to USD 1,130.20 million by 2027, and is expected to grow at a CAGR of 3.2% from 2020 to 2027.
Ceramic substrates can just meet the performance requirements of mid-to-high-end chips, and have been well used in mid-to-high-end products in the fields of home appliance lighting, information communication, sensors, etc. It is an ideal packaging material for a new generation of large-scale integrated circuits and power electronic modules. . The use of ceramic substrates powers the electronics and semiconductor industries.
Alumina ceramic substrate
(1) Thermal management to improve the life of CMOS image sensor
The optical signal acquisition method of the CMOS image sensor is active, and the charge generated by the photodiode will be directly amplified and output by the transistor. When dealing with rapidly changing images, the current changes frequently and the flow increases causing it to overheat. It affects the life and reliability of the CMOS image sensor. Due to the small size of the CMOS image sensor, most of the heat cannot be dissipated from the surface. If you want to achieve better heat dissipation, you can only start from the substrate. With its high thermal conductivity (20~27W/m.K), Slitton‘s alumina ceramic substrate can meet the high heat dissipation requirements of CMOS image sensors and further extend the product life cycle.
(2) Reliable performance to ensure the use of automotive sensors
Since the sensor in the car has been in the unique harsh environment (high temperature, low temperature, vibration, acceleration, humidity, noise, exhaust gas) for a long time, it should have the characteristics of small size and light weight, good reusability, and wide output range. With its high temperature resistance, vibration resistance, moisture resistance, and chemical corrosion resistance, ceramics can still protect the chip from corrosion even in relatively harsh environments. Whether it is practicability or reliability, ceramic substrates can bring a lot of improvement to products. There is no doubt that ceramic substrates are the guarantee of product cost performance.
(3) DPC process, giving products more possibilities
Ceramic substrates are more in line with the future development direction of high density, high precision and high reliability. It is a more feasible option and an important direction for the sustainable development of electronic packaging materials in the future.