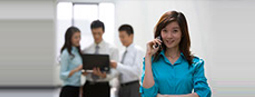
Suzhou Kaifa New Material Technology Co., Ltd.
Email:heqing@szkfxc.com
Email:sales@szbknm.com
Email:bkxc.bonnie@gmail.com
A brief introduction to the preparation and application of silicon carbide ceramics
With the advancement of science and technology in the 21st century, the development of today‘s social productive forces is concentrated in several aspects such as information, energy, materials, and biological engineering.
Silicon carbide material has developed rapidly in the field of materials due to its stable chemical properties, high thermal conductivity, low thermal expansion coefficient, low density, good wear resistance, high hardness, high mechanical strength, chemical corrosion resistance and other characteristics.
Silicon carbide ceramics started in the 1960s, before silicon carbide was mainly used for mechanical grinding materials and refractory materials. However, with the development of advanced ceramics, people are no longer satisfied with the preparation of traditional silicon carbide ceramics. Silicon ceramics are more widely used. It is now widely used in ceramic ball bearings, valves, semiconductor materials, measuring instruments, aerospace and other fields.
1. Properties of Silicon Carbide
The chemical stability of silicon carbide is closely related to its oxidation characteristics. Silicon carbide itself is easily oxidized, but after it is oxidized, a silicon dioxide film is formed, and the oxidation process is gradually hindered.
In air, silicon carbide begins to oxidize at 800°C, but slowly; as the temperature increases, the oxidation rate increases rapidly. The oxidation rate of silicon carbide is 1.6 times faster in oxygen than in air; the rate of oxidation slows down over time.
Pure silicon carbide is a colorless and transparent crystal, and industrial silicon carbide is colorless, light yellow, light green, dark green, light blue, dark blue and black, and the degree of transparency decreases in turn as the color deepens. The abrasive industry divides silicon carbide into two types: black silicon carbide and green silicon carbide according to color. Among them, colorless to dark green are classified into green silicon carbide, and light blue to black are classified into black silicon carbide. The mechanical properties of black and green silicon carbide are slightly different. Green silicon carbide is brittle, and the abrasive tools made are rich in self-sharpening; black silicon carbide is tougher, so the uses of these two silicon carbides are also different.
2. Preparation of Silicon Carbide Ceramics
1. Preparation of Ultrafine Silicon Carbide
In recent years, the preparation methods of ultrafine silicon carbide powder developed in the high-tech field are mainly classified into three types: solid-phase method, liquid-phase method and gas-phase method.
a The solid phase method mainly includes the following:
Carbothermal reduction method, Si and C direct reaction method (including high temperature self-propagating synthesis method and mechanical alloying method).
b The liquid phase method mainly includes the following:
Sol-gel methods, polymer thermal decomposition and solvothermal methods.
c The gas phase method mainly includes the following:
Vapor Reactive Deposition (CVD), Plasma Method, Laser Induced Vapor Phase Method
2. Preparation of Silicon Carbide Ceramics
Silicon carbide is a typical covalently bonded stable compound, and its low diffusion coefficient makes it difficult to achieve densification by conventional sintering methods. It must be reduced by adding some sintering aids to reduce surface energy or increase external pressure. achieve sintering.
a. Reaction Sintered Silicon Carbide Ceramics
In this method, α-SiC and C are used as raw materials, an appropriate amount of binder is added for molding and drying treatment, and then it is put into the buried material containing Si. When the green body is heated above 1400℃ in the furnace, Si around the green body melts, or penetrates into the capillary tube of the green body in a liquid state or in a gaseous state, and reacts with C in the green body to form SiC. The generated SiC gradually fills the pores in the green body, and connects the original α-SiC, and finally achieves the densification of the product and obtains the strength.
b. Hot-pressed sintered silicon carbide ceramics
Hot pressing sintering is to apply a certain pressure during the sintering process. The existence of the pressure increases the atomic diffusion rate and the sintering driving force, thereby accelerating the sintering process. However, under high pressure conditions, grains that grow directionally perpendicular to the pressure direction will appear in the sintered body. To avoid this phenomenon, the method of hot isostatic pressing can be used.
c. Pressureless sintered silicon carbide ceramics
Pressureless sintering is considered to be the most promising sintering method for SiC sintering, and SiC parts with complex shapes and large dimensions can be fabricated through the pressureless sintering process. According to the different sintering mechanisms, pressureless sintering can be divided into solid-phase sintering and liquid-phase sintering.
Third, the application of silicon carbide ceramics
a. Silicon carbide ceramic balls
Precision ball is an important component in roundness meter, gyroscope, bearing and precision measurement, and is often used as the benchmark for precision measurement, and has a very important position in precision equipment and precision machining. At present, precision balls are mainly made of metal materials, but there are problems such as poor wear resistance and large deformation under the influence of temperature. Ceramic balls have been widely used in precision bearings and other parts due to their advantages of light weight, high hardness, wear resistance, high temperature resistance, corrosion resistance, and small thermal expansion coefficient.
b. Silicon carbide abrasives
Silicon carbide is very hard and can be prepared into various grinding wheels, sandpapers and abrasives, mainly used in the machining industry. Silicon carbide has a Mohs hardness of 9.2 to 9.6, second only to diamond and boron carbide, and is a commonly used abrasive.
c. Silicon carbide matrix composites
Due to the inherent brittleness of ceramic materials, its application in high-tech fields such as aerospace has been limited, so the research on toughening of silicon carbide materials has been paid great attention. to increase the strength and modulus of the material. Silicon carbide-based composites have been widely used in high-temperature thermal structures in the aerospace field due to their high toughness, high strength, and excellent oxidation resistance.