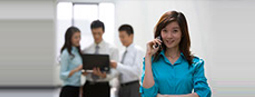
Suzhou Kaifa New Material Technology Co., Ltd.
Email:heqing@szkfxc.com
Email:sales@szbknm.com
Email:bkxc.bonnie@gmail.com
Zirconia Introduction
Zirconium dioxide (chemical formula: ZrO2) is the main oxide of zirconium. It is usually white, odorless and tasteless crystal. It is hardly soluble in water, hydrochloric acid and dilute sulfuric acid. Usually contains a small amount of thorium dioxide. Chemically inactive, with high melting point, high resistivity, high refractive index and low coefficient of thermal expansion, making it an important high temperature resistant material, ceramic insulation material and ceramic sunscreen, it is also the main raw material for artificial drills. The band gap is approximately 5-7eV.
Properties: White heavy amorphous powder. No smell. Tasteless. Soluble in 2 parts of sulfuric acid and 1 part of water, slightly soluble in hydrochloric acid and nitric acid, slowly soluble in hydrofluoric acid, almost insoluble in water. Irritating. The relative density is 5.85. Melting point is 2680 ° C. The boiling point is 4300 ° C. Hardness is second to diamond. Molecular structure: Monoclinic at low temperature, forming a tetragonal crystal form above 1100 ° C and a cubic crystal form above 1900 ° C.
1. Zirconium dioxide obtained by burning zirconium dioxide hydrate or volatile zirconium oxo acid salt is a white powder, which is insoluble in water
ZrO2 · xH2O ZrO2 + xH2O;
2. Zirconium dioxide obtained by light burning, It is relatively easy to be dissolved by inorganic acids.
ZrO2 + 4H + = Zr4 ++ 2H2O
The zirconia obtained by intense heat burning is only soluble in concentrated sulfuric acid and hydrofluoric acid, and the molten recrystallized zirconia only interacts with hydrofluoric acid;
3. Zirconium dioxide is an amphoteric oxide. It can be co-melted with alkali to form zirconate. However, zirconate is easily hydrolyzed to ZrO2 · xH2O and precipitates in the presence of water.
ZrO2 + 2NaOH = Na2ZrO3 + H2O
Na.ZrO3 + H2O = ZrO2 + NaOH;
4. Zirconium dioxide reacts with carbon and chlorine at high temperature, or reacts with carbon tetrachloride to form zirconium tetrachloride and zirconium dichloride. Get zirconium dioxide [3]
3ZrO2 + 2C + 4Cl2 = ZrCl4 + 2CO2 + 2ZrOCl2;
5. It interacts with carbon in the arc to form zirconium carbide
ZrO2 + 2C = CO2 + ZrC;
6. ZrO2 of oblique zircon type is yellow or brown monochromatic oblique crystal, which is insoluble in water, hydrochloric acid and dilute sulfuric acid, and soluble in hot concentrated hydrofluoric acid, nitric acid and sulfuric acid. Co-melt with alkali to form zirconate. Chemically very stable. Used to make advanced ceramics, enamels and refractory materials. It can be prepared by co-melting zirconite and soda ash, leaching sodium zirconate with water, interacting with hydrochloric acid to form zirconium dichloride, and calcining.
The raw materials of metal zirconium and its compounds are
used to make metal zirconium and zirconium compounds, to make refractory bricks and crucibles, high-frequency ceramics, abrasive materials, ceramic pigments and zirconates, etc.It is mainly used in piezoelectric ceramic products, daily ceramics, and refractory Materials and precious metal smelting zirconium bricks, zirconium tubes, crucibles, etc. It is also used in the production of steel and non-ferrous metals, optical glass and zirconia fibers. Also used in ceramic pigments, electrostatic coatings and baking paints. Used in epoxy resin to increase the corrosion resistance of hot salt water.
Refractory material
Zirconia fiber is a polycrystalline refractory fiber material. Due to the high melting point, non-oxidation and other high temperature characteristics of ZrO2, the ZrO2 fiber has a higher operating temperature than other refractory fiber varieties such as alumina fiber, mullite fiber, and aluminum silicate fiber. Zirconia fibers are used for a long time in an ultra-high temperature oxidizing atmosphere above 1500 ℃. The maximum operating temperature is up to 2200 ℃, and the fiber shape can be maintained even at 2500 ℃. The high temperature chemical stability, corrosion resistance, oxidation resistance, thermal shock resistance, Non-volatile and pollution-free, it is one of the top international refractory fiber materials. The resistance of ZrO2 to acid and alkali corrosion is much stronger than that of SiO2 and Al2O3. Insoluble in water, soluble in sulfuric acid and hydrofluoric acid; slightly soluble in hydrochloric acid and nitric acid. Can be co-fused with alkali to generate zirconate.
gas turbine
Plasma-sprayed zirconia thermal barrier coatings have been used in aerospace and industrial gas turbines to a great extent, and have been used in the turbine parts of gas turbines to a certain extent. Because this coating can reduce the temperature of air-cooled high-temperature parts by 50 to 200 ° C, it can significantly improve the durability of high-temperature parts, or allow the gas temperature to be increased or the amount of cooling gas required to be maintained while maintaining the temperature of high-temperature parts. Change, thereby improving the efficiency of the engine.
Ceramic materials are used
as raw materials for the kiln industry because of their large refractive index, high melting point, and strong corrosion resistance. Piezoelectric ceramic products include filters, speaker ultrasonic underwater acoustic detectors, etc. There are also daily-use ceramics (industrial ceramic glazes), zirconium bricks and pipes for precious metal melting. Nano-sized zirconia can also be used as a matrix material for polishing agents, abrasive particles, piezoelectric ceramics, precision ceramics, ceramic glazes and high temperature pigments.
Other
addition may be used to manufacture zirconium oxide gas incandescent globe, enamel, white glass, refractory crucible and the like. X-ray photography. Abrasive materials. Used together with yttrium to make light source lamps in infrared spectrometers, thick film circuit capacitor materials, and piezoelectric crystal transducer formulations.
Production method
1. Zirconium oxychloride pyrolysis method: zircon and caustic soda are melted at 650 ° C, and the molten body is leached with hot water, and the silicon is in the form of sodium silicate and separated from sodium zirconate. After treatment with sulfuric acid, a zirconium sulfate solution is obtained. After further removing impurities, ammonia water is added to precipitate zirconium hydroxide. Add hydrochloric acid to dissolve zirconium hydroxide to obtain zirconium oxychloride. After evaporation, concentration, cooling, crystallization, crushing, and baking, the finished zirconium dioxide can be obtained. In addition, the easily purified zirconium compound can be thermally decomposed or oxidized to produce high purity Zirconia.
2. Colloid method: In the zirconia solution, a silica sol is added to prepare a colloid solution, which is formed by a blowing and drawing method, and sintered into fibers after drying.
3. Extrusion method: The zirconia sol or zirconia particles and thickener are made into a billet. The billet is extruded from the mouth of the model and formed into filaments by using hydraulic pressure or the advancing effect of a spiral reamer, and then sintered to solidify Fibres. The fiber obtained by this method is relatively thick and the strength of the fiber is also low.
4. Dipping method: first immerse the viscose yarn or the entire fabric in a zirconium hydroxide solution for a long time to swell the viscose fibers, and then pyrolyze and calcinate to obtain zirconia fibers with a certain tensile strength.
5. Hydrolysis method: Use zirconyl oxychloride as raw material to prepare high-purity ultra-fine zirconium dioxide, hydrolyze 0.2 ~ 0.3 mol / L high-purity zirconyl chloride solution with deionized water, and boil the zirconium oxychloride solution for a long time Hydrogen chloride generated by hydrolysis is continuously evaporated and removed. The hydrolysis reaction is carried out for more than 50 hours under boiling, and then filtered, washed with deionized water, dried, calcined and crushed to obtain a product.
6. High-temperature hydrolysis method: spray 1 mol / L of high-purity zirconium oxychloride solution into a decomposition furnace at a temperature of 1000 ℃, the tiny zirconia oxychloride droplets are first evaporated, and then hydrolyzed to form zirconium dioxide. The decomposed zirconium dioxide is collected by a cyclone, and then pickled, washed and dried to obtain a product.
7. Sol-gel method: add alcohol and water to zirconium alcohol [ZrO (C3H7) 4], and then add a catalyst. After being fully mixed, it begins to decompose, and it is allowed to gel and become a thick liquid. Dry and reheat to 500 ~ 1000 ℃, high temperature fiberization and firing to obtain the product.
8. Alcohol hydrolysis method: Zirconium tetrachloride, ammonia and propanol are used as raw materials to prepare high-purity ultra-fine zirconium dioxide. Zirconyl alcohol is prepared by reacting high-purity zirconium tetrachloride with propanol and ammonia at 5 ° C in the presence of a benzene solvent The salt is separated by filtration to remove ammonium chloride, and then hydrolyzed to precipitate and filtered, and dried, calcined, and pulverized to obtain the product at a temperature of not less than 100 ° C. The hydrolysis conditions directly affect the particle size, shape, and aggregation of the product. This method can produce ZrO2 with uniform particle size and shape and a single structural phase.
9. Recrystallize zirconium oxychloride (ZrCl2O · 8H2O) with hydrochloric acid or methanol, and calcine at high temperature to obtain a finished product.
10. The tetraalkoxyzirconium is purified by distillation, and the steam is decomposed at 350 ~ 500 ° C to obtain a finished product.
11. Purify zirconium tetrachloride by distillation, and react the vapor with excess oxygen at 1200 ° C to obtain zirconium dioxide.
Stable zirconia for refractory materials used in the process industry is mostly prepared by electrofusion method. Carbon and stabilizer calcium oxide are added in the zircon electrofusion process. While removing silicon, zirconia and calcium oxide react to form a solid solution, and then crushed and granulated to obtain stable zirconia. The stabilized and partially stabilized zirconia used in fine ceramics is generally made by the wet method. At present, the most mature and commonly used method is the neutralization precipitation method, and its preparation process is shown in the figure. Dissolve the purified zirconium oxychloride with pure water, remove insoluble matter by filtration, adjust the zirconium concentration in the solution, and add the required amount of yttrium chloride solution (or other rare earth metal or alkaline earth metal chloride solutions), then add ammonia water Neutralize the precipitate. After the precipitate was washed with hot water, it was filtered, dried and calcined. The calcined product can be pulverized to obtain ultra-fine stable zirconia powder.
Partially stabilized zirconia is obtained by controlling the amount of stabilizer added to make it insufficient to achieve complete stability. Partially stabilized zirconia has high strength and thermal shock resistance, and has a wide range of uses in structural ceramics.
Zirconia ceramics are white, yellow or gray with impurities, and generally contain HfO2, which is not easy to separate. There are three crystalline states of pure ZrO2 under normal pressure. The production of zirconia ceramics requires the preparation of powders with high purity, good dispersion properties, ultrafine particles, and narrow particle size distribution. There are many methods for preparing zirconia ultrafine powders. The purification of zirconia mainly includes chlorination and thermal decomposition methods, and alkali metals. Oxidative decomposition method, lime melting method, plasma arc method, precipitation method, colloid method, hydrolysis method, spray pyrolysis method, etc.
Pure ZrO2 is white, yellow or gray when containing impurities, and generally contains HfO2, which is not easy to separate. The world‘s proven zirconium resources are about 19 million tons, and zirconia is usually made by purifying zirconium ore. Pure ZrO2 has three crystal states under normal pressure: Monoclinic zirconia (m-ZrO2), Tetragonal zirconia (t-ZrO2) and Cubic zirconia (c-ZrO2). Three crystal forms exist in different temperature ranges and can be converted to each other:
Temperature density
Monoclinic zirconia (m-ZrO2) <950 ℃ 5.65g / cc
Tetragonal zirconia (t-ZrO2) 1200-2370 ℃ 6.10g / cc
Cubic zirconia (c-ZrO2)> 2370 ℃ 6.27g / cc The
above three crystal states have different physical and chemical properties. Application In order to obtain the required crystal form and performance, different types of stabilizers are usually added to make different types of zirconia ceramics, such as partially stabilized zirconia (PSZ). When the stabilizers are CaO, MgO, Y2O3 , Expressed as Ca-PSZ, Mg-PSZ, Y-PSZ, etc., respectively. Tetragonal zirconia composed of metastable t-ZrO2 is called tetragonal zirconia polycrysta (TZP). When the added stabilizer is Y2O3, CeO2, it is expressed as Y-TZP, Ce-TZP, etc., respectively.
Production process editing
The molding of zirconia ceramics includes dry pressing, isostatic pressing, grouting, hot die casting, cast molding, injection molding, plastic extrusion molding, colloidal solidification molding, etc. The most widely used are injection molding and dry pressing.
(1) Grouting The
grouting molding process includes physical dehydration and chemical agglomeration. Physical dehydration removes moisture from the slurry through the capillary action of a porous gypsum mold. The chemical agglomeration process is due to the dissolution of CaSO4 on the surface of the gypsum mold. The generated Ca2 + increases the ionic strength in the slurry, causing flocculation of the slurry. Under the action of physical dehydration and chemical agglomeration, ceramic powder particles are deposited on the wall of the gypsum mold. Grouting is suitable for the preparation of large-scale ceramic parts with complex shapes, but the quality of the green body, including the shape, density, and strength, is poor. Workers have high labor intensity and are not suitable for automated operations.
(2) Hot die casting
Hot die-casting is to mix ceramic powder and binder (paraffin) at a higher temperature (60 ~ 100 ° C) to obtain a slurry for hot-die casting. The slurry is injected into a metal mold under the action of compressed air to maintain pressure. Cooling and demoulding to obtain a wax blank. The wax blank is dewaxed under the protection of an inert powder to obtain a plain green, which is then sintered into porcelain at high temperature. The size of the green compact formed by hot die casting is accurate, the internal structure is uniform, the mold wear is small, and the production efficiency is high, which is suitable for various raw materials. The temperature of the wax slurry and the mold needs to be strictly controlled, otherwise it will cause under-injection or deformation, so it is not suitable for manufacturing large parts. At the same time, the two-step firing process is more complicated and the energy consumption is higher.
(3) Casting molding
Casting molding is to fully mix ceramic powder with a large amount of organic binders, plasticizers, dispersants, etc. to obtain a viscous slurry that can flow, and add the slurry to the hopper of the casting machine. The thickness is controlled by a scraper, and it flows out to the conveyor belt through the feeding nozzle, and the film blank is obtained after drying. This process is suitable for preparing thin film materials. In order to obtain good flexibility, a large amount of organic substances are added, and strict control of process parameters is required, otherwise defects such as peeling, streaks, low film strength, or difficulty in peeling are likely to be caused. The organic substances used are toxic and will cause environmental pollution. As far as possible, non-toxic or less toxic systems should be used to reduce environmental pollution. [1]
In addition to the dry pressing-based molding technology, products manufactured by other processes must be degreased and discharged before being sintered in the furnace, because other processes except dry pressing will be formed in zirconium during molding. A certain proportion of plasticizers are added to the powder. These plasticizers must be removed after the product is formed, otherwise it will have a serious impact on the quality of the sintered product. Plasticizers are mainly composed of paraffin and other polymer materials. These materials are required to exhibit good plasticity and fluidity at a certain temperature, and have certain toughness and strength at room temperature.
Sintering
sintering method is generally zirconia ceramics may be employed are: ⑴ pressureless sintering, ⑵ hot press sintering and reaction hot pressing sintering, ⑶ hot isostatic pressing sintering (HIP), ⑷ microwave sintering, ⑸ ultrahigh pressure sintering, ⑹ discharge plasma Sintering (SPS), ⑺ in situ pressure forming sintering, etc. It is usually dominated by pressureless sintering.
In terms of structural ceramics, zirconia ceramics are widely used in the field of structural ceramics because of their advantages such as high toughness, high bending strength and high wear resistance, excellent thermal insulation properties, and thermal expansion coefficient close to that of steel. Mainly include: Y-TZP grinding balls, dispersion and grinding media, nozzles, ball valve ball seats, zirconia molds, miniature fan shafts, optical fiber pins, optical fiber sleeves, wire drawing dies and cutting tools, wear-resistant tools, clothing buttons, Cases and straps, bracelets and pendants, ball bearings, light golf bats and other wear-resistant components at room temperature.
In functional ceramics, its excellent high temperature resistance is used as induction heating tubes, refractory materials, and heating elements. Zirconia ceramics have sensitive electrical performance parameters and are mainly used in fields such as oxygen sensors, solid oxide fuel cells (SOFC), and high-temperature heating elements. ZrO2 has a relatively high refractive index (N-21 ^ 22), adding certain coloring elements (V2O5, MoO3, Fe2O3, etc.) to ultra-fine zirconia powder, which can be made into colorful translucent polycrystalline ZrO2 Like a natural gemstone, it flashes a colorful light and can be made into various decorations. In addition, zirconia is widely used in thermal barrier coatings, catalyst carriers, medical, health care, refractory materials, textiles and other fields.
Zirconia is a special material. The toughening method is mainly achieved by the phase change of zirconia!
Pure zirconia is a white solid, which appears gray or light yellow when it contains impurities, and it can show various other colors by adding a developer. Pure zirconia has a molecular weight of 123.22, a theoretical density of 5.89 g / cm3, and a melting point of 2715 ° C. It usually contains a small amount of hafnium oxide and is difficult to separate, but it has no significant effect on the performance of zirconia. Zirconia has three crystal forms: monoclinic, tetragonal, and cubic crystal phases. At normal temperature, zirconia appears only as a monoclinic phase. When heated to about 1100 ° C, it changes into a tetragonal phase. When heated to a higher temperature, it turns into a cubic phase. Because a large volume change occurs when the monoclinic phase changes to a tetragonal phase, and a large volume change occurs in the opposite direction when cooling, it is easy to cause product cracking, which limits the application of pure zirconia in high temperature fields . However, after the stabilizer is added, the tetragonal phase can be stabilized at normal temperature, so no sudden change in volume will occur after heating, which greatly expands the application range of zirconia. The raw material used as a stabilizer in the market is mainly yttrium oxide.
Like diamond, cubic zirconia is cubic crystal. Under normal pressure, the stable crystal of zirconia is mono-clinic. Therefore, in the process of forming a cubic zirconia, it is necessary to add a metal oxide with a molecular weight of 10 to 15% (usually yttrium oxide or Calcium oxide) as a stabilizer. Different production methods will add different amounts of stabilizers, so the physical and optical characteristics of cubic zirconia will be slightly different.
Cubic zirconia has a high density, with a specific gravity of 5.6 to 6.0. Its hardness is 8.5, although it is lower than diamond, but it has exceeded most natural gems. Its refractive index is 2.15 to 2.18, and the surface is diamond-glossy. The dispersion index reaches 0.058 to 0.066, exceeding diamonds. Cubic zirconia has no cleavage, and the fracture is a conchoidal fracture, which is fragile. It shows yellow and yellow-green fluorescence under short-wave UV, but not obvious under long-wave UV.
Cubic zirconia is very close to diamond (diamond) optically, and ordinary people may not be able to distinguish the two. However, there are still some differences under the microscope:
dispersion: the dispersion of cubic zirconia is 0.060, which is higher than 0.044 of diamond. So cubic zirconia looks more brilliant than diamond.
Hardness: The Mohs hardness of cubic zirconia is 8.5 to 9.0, and that of diamond is 10.
Specific gravity: Cubic zirconia is 1.7 times heavier than diamond. But this feature can only be used to separate unset stones.
Defects: The cubic zirconia produced is basically flawless inside and out. Natural diamonds are rarely completely flawless inside and out.
Refractive index: The refractive index of cubic zirconia is 2.176, which is slightly lower than that of diamond‘s 2.417.
Cutting: Due to the different refractive index, the cutting of cubic zirconia is slightly different from that of diamond, which can be found by careful observation under a magnifying glass.
Color: Diamonds that are completely colorless are very rare and usually have a light yellow color. But cubic zirconia can be made into the highest grade of diamond, namely D color.
Heat transfer: The thermal conductivity of cubic zirconia and diamond is at two extremes. Cubic zirconia is an excellent thermal insulation material and can be used as thermal insulation for jet engines. Diamond is one of the best thermal conductors, and its thermal conductivity exceeds copper. With the right equipment, this property can best distinguish the two.