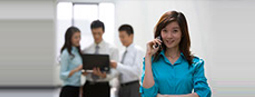
Suzhou Kaifa New Material Technology Co., Ltd.
Email:heqing@szkfxc.com
Email:sales@szbknm.com
Email:bkxc.bonnie@gmail.com
Stability of zirconia material
The martensitic transformation of zirconia is one of the important topics widely studied in the field of ceramics, and has been successfully applied in the toughening and strengthening of structural ceramics. Refractory materials generally serve under thermal cycling conditions. Unlike structural ceramics used at room temperature, their thermal shock resistance is an important performance indicator. According to the phase transition characteristics of zirconia, the idea of using zirconia phase transition to improve the thermal shock resistance of zirconia refractories was proposed.
The martensitic transformation of zirconia can significantly improve the fracture toughness of structural ceramics, which has been extensively and deeply studied. The service conditions of refractory materials are different from structural ceramics used at normal temperature.The stress-induced phase transformation toughening mechanism at high temperature loses its effect.Therefore, the effect of zirconia phase transformation on the performance of refractory materials (especially the thermal shock resistance) must show a different Features. Existing studies have shown that the volume effect accompanying phase transition is easy to cause the fracture of the material on the one hand, and micro-cracks can be generated in the local area of the material on the other hand to improve the material‘s resistance to thermal shock damage. It can be seen that the effect of zirconia phase transition on the thermal shock resistance of refractory materials is dual.It is necessary to carefully analyze the characteristics of zirconia phase transition, to clarify the internal relationship between it and the thermal shock resistance of the material, and to make a comprehensive evaluation. To take advantage of phase change to improve the thermal shock resistance of refractory materials. Zh
Zirconium oxide phase transition characteristics Zirconia has three main crystal forms, namely monoclinic, tetragonal and cubic crystal forms. The transformation relationship between them can be expressed as follows: The phase transition between monoclinic and tetragonal phases is of great significance in the development of ceramic materials. WoltenGM first pointed out that this phase changed to a martensite phase. Previous studies have shown that this phase transition has the following characteristics: (1) athermal phase transition (athermal), that is, the amount of phase transition is only related to temperature, and has nothing to do with time. (2) Thermal hysteresis, that is, the phase transition occurs within a certain temperature range, the temperature of the monoclinic phase to tetragonal phase is 1170 ℃, and the temperature of the tetragonal phase to monoclinic phase is in the range of 850 ~ 1000 ℃, The phase transition temperature lags about 200 ° C. (3) The phase transition is accompanied by a volume effect of about 3% to 5% and considerable shear deformation. From t2ZrO2 phase to m2ZrO2 volume expansion, otherwise volume shrinkage occurs. (4) The phase transition has no diffusion reaction, and the phase transition speed can reach the speed of sound in the solid, which is faster than the speed of crack propagation. This feature makes it possible to improve the toughness of ceramic materials by using phase transitions to prevent crack growth. In addition, this speed is faster than the changes in temperature and thermal stress during rapid cooling and rapid heating of the material. It is possible to use its unique volume effect to relieve thermal stress, which can improve the thermal shock resistance of the material. 5) It has particle size effect. When the particles are smaller than a certain critical size, t2 zirconia can be retained to room temperature without phase change. (6) Adding a stabilizer can suppress phase change. Adding magnesia, calcium oxide, yttrium oxide, etc. to zirconia can make zirconia stably exist as t2 zirconia or c2 zirconia. (7) The phase transition is affected by the state of mechanical constraints. When under compressive stress, the tϖm phase transition will be suppressed; otherwise, the phase transition is favorable.
Thermal shock resistance refers to the ability of a material to withstand rapid changes in temperature without being damaged. When there is a temperature gradient or thermal expansion mismatch between different phases, thermal stress will be generated in the material. According to the theory of thermoelasticity, the surface of the material will be in a state of tensile stress during cooling. When the tensile stress exceeds the limit of tensile strength, the material will fracture. Thermal shock on the one hand causes the strength of the ceramic material to decay, on the other hand induces cracks in the material, which accelerates the spalling and erosion of the material, which is an important cause of damage to the ceramic material, especially for refractory materials used under thermal shock cycle conditions in this way. There are generally several ways to improve the thermal shock resistance of refractory materials: (1) Design a large number of micro pores in the material. These micro pores can be used as a "concentrator" for thermal stress, to accommodate a certain degree of deformation and relieve thermal stress. Role. However, the existence of micro pores severely reduces the corrosion resistance of the material. This method will be limited under the use conditions that require high thermal shock resistance and erosion resistance of the material. (2) The glass phase in the refractory material softens and plastically deforms at higher temperatures, and it can also play a role similar to micro pores. Similarly, the presence of the glass phase is also detrimental to the high temperature mechanical properties and erosion resistance of the refractories. Therefore, the glass phase is always minimized or eliminated in the preparation of refractory materials. (3) Microcrack toughening. As is known to all, the introduction of a certain density of microcracks in ceramic materials can significantly improve the toughness of the material, thereby improving the thermal shock resistance of the material. The mechanics of fracture has been explained theoretically. Predecessors have used microcrack toughening to improve the thermal shock resistance of refractory materials. The effect of fused mullite-zirconia aggregates on the thermal shock resistance of refractory materials was studied in the alumina matrix. Microcracks are generated in the refractory material, which greatly improves the thermal shock resistance of the material. Zh
In addition, GarvieetalRC [5] proposed a method for designing advanced refractory materials using monoclinic zirconia particles. The method is to introduce monoclinic zirconia particles with an average size of 13 μm into an inert brittle matrix, and make these particles uniformly distributed to make a composite material close to the theoretical density. This material has excellent thermal shock resistance. Its toughening mechanism has nothing to do with phase transition, but is caused by the thermal stress caused by the significant anisotropic expansion of monoclinic zirconia particles, which results in the formation of latent microcracks in the matrix.
According to the characteristics of zirconia phase transition and the principle of thermal shock resistance of refractory materials, the basic idea of zirconia phase transition design to improve the thermal shock resistance of refractory materials is proposed as follows: The characteristics of zirconia phase transition allow the size of The solution composition, the stress state, and the existence mode adjust the amount of phase change and the phase change temperature range. During the refractory cooling process, temperature and thermal stress gradients are generated from the surface of the test piece to the inside, that is, the temperature profile and thermal stress profile. The surface tension of the test specimen generates tensile stress. The larger the surface tensile stress, the more favorable the tϖm phase transition. The temperature of the central part of the test piece is high, and it is in a state of compressive stress, which has a suppressive effect on the phase change and the phase variable is small. Therefore, the amount of phase change from the surface of the test piece to the inside is controlled by the temperature profile and thermal stress profile. The relationship between them can be schematically illustrated in FIG. 1.
Zh
Phase changes are automatically adjusted by changes in temperature and thermal stress, and the phase change volume expands, which relieves tensile stress and effectively reduces thermal stress-induced fracture. Therefore, it is possible to design a certain amount of t2 zirconia to undergo a phase change at an appropriate temperature range (in which the thermal stress is the largest). The positive volume effect accompanying the phase change macroscopically cancels the surface volume shrinkage caused by cooling, which eases surface tension Stress, which reduces the possibility of thermal stress fracture on the surface. On the other hand, the volume fraction of t2 zirconia particles (volume percentage of t2 zirconia particles per unit volume), particle size distribution, and existence mode (intergranular or intragranular) are designed to make the phase transition induced uniform and have a certain Density of microcracks. These microcracks can not only synergistically toughen in a thermal shock environment, but also not cause polymerization, and improve the thermal shock resistance of refractory materials.
Commonly used varieties of ordinary and special refractories
First, acid refractory
There are silica bricks and clay bricks with larger amounts of concrete. Silica brick is a silicon product containing more than 93% SiO2. The raw materials used are silica, waste silica brick and so on. Silicon bricks have strong resistance to acid slag erosion, but are susceptible to alkaline slag erosion. Its load softening temperature is very high, close to its refractory degree. After repeated calcination, the volume does not shrink, and even slightly expands, but it is resistant to refractory abrasives. Poor seismicity. Silicon brick is mainly used in coke ovens, glass melting furnaces, acid steelmaking furnaces and other thermal equipment. Clay bricks contain 30% to 46% alumina. It uses refractory clay as the main raw material, with a fire resistance of 1580 to 1770 ° C and good thermal shock resistance. It belongs to weakly acidic refractory materials, has corrosion resistance to acidic slag, and is widely used. Is the largest production of a class of refractory materials.
Second, neutral refractory
The main crystalline phases in high-aluminum products are mullite and corundum. The content of corundum increases with the increase of alumina content. Corundum products containing more than 95% of alumina are a wide range of high-quality refractory materials. Chrome brick is mainly made of chrome ore, and the main crystal phase is chromite. Its corrosion resistance to steel slag is good, but its thermal shock resistance is poor, and the high temperature load deformation temperature is low. Chromium-magnesium bricks made of chrome ore and magnesia in different proportions have good thermal shock resistance, and are mainly used as alkaline open-hearth roof bricks. Carbonaceous products are another type of neutral refractory materials. According to the composition of the carbon-containing raw materials and the mineral composition of the products, they are divided into three types: carbon bricks, graphite products and silicon carbide products. Carbon bricks are made from high-grade petroleum coke, tar and asphalt are used as the binder, and fired under the condition of 1300 ℃ isolated from air. Graphite products (except natural graphite) are made by using carbonaceous materials in an electric furnace through graphitization at 2500-2800 ° C. Silicon carbide products use silicon carbide as the raw material, and add clay, silicon oxide and other binders to sinter at 1350 ~ 1400 ° C. The silicon carbide and silicon powder can also be made into silicon carbide products in a nitrogen atmosphere in an electric furnace. The refractory and abrasive carbon products have low thermal expansion coefficient, high thermal conductivity, good thermal shock resistance, and high temperature strength. It does not soften under long-term use at high temperature, is not affected by any acid and alkali, has good salt resistance, and is not affected by the corrosion of metals and slag. It is lightweight and is a high-quality high-temperature resistant material. The disadvantage is that it is easy to oxidize at high temperature, and it is not suitable to use in an oxidizing atmosphere. Carbon products are widely used in high-temperature furnace linings (hearth, hearth, bottom of furnace body, etc.) and linings for melting non-ferrous metal furnaces. Graphite products can be used as liners for reaction tanks and petrochemical autoclaves. Silicon carbide and graphite products can also be made into crucibles for smelting copper alloys and light alloys.
3. Alkaline refractory
Represented by magnesium products. It contains more than 80% to 85% of magnesia, with periclase as the main crystal phase. The main raw materials for producing magnesia bricks are magnesite and seawater magnesia, which is obtained by calcining magnesium hydroxide extracted from seawater at high temperature. Good resistance to alkaline slag and iron slag. The melting point of pure magnesia is as high as 2800 ° C. Therefore, the fire resistance of magnesia bricks is higher than that of clay bricks and silica bricks. Since the mid 1950s, due to the use of oxygen-blown converter steelmaking and the use of alkaline open hearth furnaces, the production of basic refractory materials has gradually increased, while the production of clay bricks and silicon bricks has decreased. Alkaline refractories are mainly used in open hearth furnaces, oxygen-blown converters, electric furnaces, non-ferrous metal smelting, and some high-temperature thermal equipment.
Fourth, oxide materials
Rhenium, such as alumina, lanthanum oxide, beryllium oxide, calcium oxide, zirconia, uranium oxide, magnesium oxide, cerium oxide, and thorium oxide, has a melting point of 2050-3050 ° C.
Five, refractory compound materials
Such as carbides (silicon carbide, titanium carbide, tantalum carbide, etc.), nitrides (boron nitride, silicon nitride, etc.), borides (zirconium boride, titanium boride, hafnium boride, etc.), silicides (disilicide Molybdenum, etc.) and sulfides (rhenium sulfide, cerium sulfide, etc.). Their melting points are 2000 to 3887 ° C. Among them, the most refractory is carbide.
Six, high temperature composite materials
For example, cermets, high-temperature inorganic coatings, and fiber-reinforced ceramics.