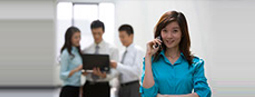
Suzhou Kaifa New Material Technology Co., Ltd.
Email:heqing@szkfxc.com
Email:sales@szbknm.com
Email:bkxc.bonnie@gmail.com
Ceramic sintering process principle and method
Ceramic sintering is a general term for the compaction process and phenomenon of green body at high temperature. As the temperature rises, the ceramic body has powder particles that are larger than the surface and have a higher surface energy. They try to change to the direction of reducing the surface energy, and continue to migrate substances, and the grain boundaries move accordingly, and the pores are gradually eliminated, causing shrinkage. Make the body into a dense porcelain body with a certain strength. The driving force for sintering is surface energy. Sintering can be divided into sintering with liquid phase participation and pure solid phase sintering. The sintering process is very important for ceramic production. In order to reduce the sintering temperature and expand the firing range, some additives are usually added as fluxes to form a small amount of liquid phase to promote sintering. Such as adding a small amount of silica to promote the sintering of barium titanate ceramics; and adding a small amount of magnesium oxide, calcium oxide, and silica to promote the sintering of alumina ceramics. (Baidu Encyclopedia)
Sintering overview
Sintering is a technology that uses thermal energy to densify a powder green body. The specific definition refers to the process of densification of a porous body under high temperature conditions with reduced surface area, reduced porosity, and improved mechanical properties (mechanical strength, etc.). A series of physicochemical changes occur during the sintering process of the green body, such as expansion, contraction, gas generation, liquid phase appearance, the disappearance of the old crystal phase, and the formation of new crystal phase. At different temperatures and atmospheres, the content and degree of changes are also different, resulting in different crystal phase compositions and microstructures, which determine the different quality and performance of ceramic products. The glaze layer on the surface of the green body also undergoes various physical and chemical changes during the sintering process, and finally forms a glassy substance, thereby having various physical and chemical properties and decorative effects.
Driving force of sintering
The green body has only point contact between particles, and the strength is very low. Although there is no external force or chemical reaction during sintering, the point contact particles can be tightly formed into a hard and high-strength porcelain body.
What is the power of sintering? It is the surface energy of powder. During the preparation process, mechanical properties such as crushing, ball milling or other energy are stored in the powder in the form of surface energy, causing many lattice defects on the surface of the powder and making the powder have higher activity. Excess surface energy of powder: It is the driving force of sintering (the total surface area after sintering is reduced by more than 3 orders of magnitude). Sintering cannot be performed automatically. The powder must be heated and supplemented with energy before it can be transformed into an unsintered body. In addition to the driving force, there must also be a substance transfer process, so that the pores are gradually filled, so that the green body becomes dense by transportation.
1. Evaporation and condensation
2. Diffusion
3. Viscous flow and plastic flow
4. Dissolution and precipitation may have several mass transfer mechanisms at work when sintering is too heavy. Under certain conditions, a certain mechanism is working, and the conditions change, and the mechanism of the guiding function may change accordingly.
Solid-phase sintering process and mechanism
Solid phase sintering can generally be expressed in three stages. The initial stage is mainly represented by particle shape changes; the intermediate stage is mainly represented by pore shape changes; and the final stage is mainly represented by pore size reduction. The main mass transfer method of solid phase sintering is diffusion mass transfer. There are surface diffusion, grain boundary diffusion and volume diffusion. Not every diffusion mass transfer can cause the material to shrink or reduce the porosity. Substances are transferred from the surface to the neck by surface diffusion or lattice diffusion, without causing a decrease in the center-to-center spacing, causing shrinkage and reducing the porosity. The mass transfer of particles from the particle volume or from the grain boundary to the neck will cause the shrinkage of the material and the disappearance of the pores, which will actually lead to the densification of the material. The composition of the material, particle size, microstructure (pores, grain boundaries), temperature, atmosphere and additives will affect the diffusion and mass transfer, which in turn will affect the sintering of the material.
Liquid sintering process and mechanism
Liquid-phase sintering (liquid-phase sintering) refers to sintering a green body containing multiple powders, the sintering temperature of which is at least higher than the melting temperature of one of the powders, so that the liquid phase sintering process occurs during the sintering process. The advantage of liquid phase sintering is that it can improve the driving force of sintering and can produce ceramic composite materials with controlled bystander structure and optimized performance. Flow mass transfer is much faster than diffusion mass transfer, and the sintering rate is high, resulting in a dense sintered body at lower temperatures. Specific conditions for liquid phase sintering: 1. Wetting of liquid phase relative to solid phase particles 2. Solid phase has considerable solubility in liquid phase 3. Liquid phase has suitable year 4. With considerable amount of liquid phase during liquid phase sintering process The pores are excluded. In the middle of sintering, the continuous pore channels start to shrink to form closed pores. After the pores are closed, they enter the final stage. At the end of sintering, several processes can occur simultaneously, including the growth and coarsening of grains and pores, the diffusion of liquid phase components into the solid phase, and the formation of reaction products between the solid phase, liquid phase, or gas phase. Liquid phase sintering is widely used in structural ceramics and electronic ceramics.
Featured sintering method
1. Hot pressing sintering
2. Hot isostatic pressing
3. Spark plasma sintering
4. Microwave sintering
5. Reaction sintering
6. Explosive sintering
The forming pressure required for hot pressing sintering is only 1/10 of the cold pressing method, which reduces the sintering temperature and shortens the sintering time, inhibits the growth of grains, and can obtain products with good mechanical properties and electrical properties. It can produce complex sizes and precise sizes. Products, the shortcomings are also obvious, low production efficiency and high cost.
The hot isostatic pressing process can be completed at a lower sintering temperature, which suppresses many adverse reactions or changes at high temperatures, can reduce or eliminate sintering aids, and obtain a uniform and dense sintered body, which can reduce or eliminate the sintered body The remaining pores increase the density and strength of the material, accurately control the size and shape of the product, and avoid cutting and other processes.
Sintering equipment
Sintering is carried out in thermal engineering equipment, where thermal engineering equipment refers to advanced ceramic production kilns and ancillary equipment. There are many types of sintered ceramic kilns. The same product can be fired in different types of kilns, and the same kiln can also sinter different products. The main commonly used ones are batch kilns, continuous kilns and auxiliary equipment. Intermittent kilns can be divided into electric furnace, high temperature inverted flame kiln, shuttle kiln and bell kiln according to their functions. There are many classification methods for continuous kilns. According to the conveying method of products, they can be divided into tunnel kilns, high-temperature push plate kilns and roller kilns. Compared with traditional batch kilns, continuous kilns have continuous operability and are easy to achieve mechanization, which greatly improves labor conditions and reduces labor intensity and energy consumption.
Determination of the best firing parameters
The firing system includes temperature system, atmosphere system and pressure system. The key to the performance of the product is the temperature and its relationship with time and the atmosphere during firing. Among them, the temperature system and the atmosphere system need to be determined according to different production requirements, and the pressure system is to ensure that the kiln is fired according to the required temperature system and atmosphere system. The basis for formulating the firing system: based on the chemical composition of the green glaze and its physical and chemical changes during the firing process; based on the type, size, shape and thickness of the green body; based on the structure, type and fuel of the kiln The type, kiln loading method and kiln density are based on; based on the successful firing experience of similar products. The determination of temperature system includes parameters such as heating rate, firing temperature, holding time and cooling rate. Through the change of the properties of the flying billet during the firing process, it is preliminary obtained that the billet can be allowed to rise and fall at various temperature or time stages (phase diagram, differential heat-weight loss, thermal expansion, high-temperature phase analysis, existing sintering curve, etc.) . Heating rate: low temperature stage, oxidative decomposition stage, high temperature stage. Sintering temperature and holding time: mutual restraint, can compensate each other to a certain extent, with the purpose of primary grain development and maturity, obvious grain boundaries, no significant secondary grain growth, uniform shrinkage, dense and low energy consumption for the purpose of . The cooling rate, as the furnace cools, quickly cools. The determination of the atmosphere system depends on the blank. Oxidizing atmosphere, neutral atmosphere or reducing atmosphere can be used during firing. The firing atmosphere at each stage must be determined according to the raw material properties and different requirements of the product. Blank evaporation period , no special atmosphere requirements; oxidative decomposition and the crystal transition period, sufficient to make the blank oxidative decomposition using an oxidizing atmosphere; Vitrification of porcelain, earthenware large are employed firing in oxidizing atmosphere, the fired porcelain Success can be divided into two atmospheres: oxidizing atmosphere and reducing atmosphere. Porcelain fired in a reducing atmosphere must have a strong oxidizing atmosphere with medium heat insulation before the reduction begins. At this time, a strong oxidizing atmosphere is used, a strong oxidizing atmosphere is used in the early stage of reduction, and a weak reducing atmosphere is used in the later stage of firing.The determination of the pressure system, the pressure system plays a role in ensuring the temperature and atmosphere system. The pressure distribution of the whole kiln is determined according to factors such as the structure of the kiln, the type of combustion, product characteristics, firing atmosphere and kiln density. In the inverted flame kiln, the most important thing is to form a slight negative pressure in the flue, and the bottom of the kiln is at zero pressure. The pre-heat zone and firing zone of the tunnel kiln are under negative pressure, and the cooling zone is generally operated under positive pressure.
Source of information:
This information originates from the Internet for academic exchange only. If infringement please contact us to delete immediately