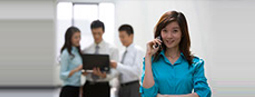
Suzhou Kaifa New Material Technology Co., Ltd.
Email:heqing@szkfxc.com
Email:sales@szbknm.com
Email:bkxc.bonnie@gmail.com
Quality products
01 Hexagonal boron nitride
The hexagonal boron nitride products produced by Hyflux are sintered at 1800-2000℃, with high crystallinity and more uniform particle size. The high crystallinity hexagonal boron nitride has thermal conductivity, insulation, lubrication, high temperature resistance and corrosion resistance to molten metal, etc. All performances are better than ordinary products. It can be used in various high-end fields, including aerospace, electronics, cosmetics, and thermally conductive materials .
02 Boron nitride ceramics
Product features and advantages:
Adopt international advanced technology high-temperature boron nitride raw materials to ensure the purity of materials and high temperature resistance.
Using cold isostatic pressing and bi-directional hot pressing sintering process, the material has high density and long service life.
Stable and mature production technology and process, without adding any binder, to ensure the stability of the material.
typical application:
High-purity boron nitride crucibles for molten metals; crucibles and burn-in plates for sintering ceramics and powders such as nitride phosphors, silicon nitride, aluminum nitride; high-temperature furnace electrode insulation and protection tubes; nitrogen for polycrystalline silicon ingot furnaces Boron Insulated Components.
03 Boron nitride composite ceramics
Product features and advantages:
Unique process formula, optimized composition structure, the material has excellent thermal shock resistance, corrosion resistance, creep resistance and other properties.
Adopting the international advanced vacuum hot pressing sintering method, the material structure is delicate, the density is high, and it has superior physical properties.
It does not react with molten metal at high temperature, does not wet or stain, and is widely used in various molten metal contact applications.
typical application:
Boron nitride horizontal continuous casting separation ring; boron nitride thin strip continuous casting side sealing plate; amorphous, nanocrystalline with boron nitride nozzle, special metal powder nozzle and guide tube.
04 Boron nitride coating
Features:
Product environmental protection characteristics: boron nitride is environmentally friendly material, non-toxic, zero pollution.
Chemical characteristics: non-sticking in high temperature environment, preventing metal corrosion and adhesion tools.
Product features: special formula, water-based matrix, easy to use.
05 Zirconia ceramics
Product features and advantages:
Pure ZrO2 is white, yellow or gray when it contains impurities, and generally contains HfO2, which is not easy to separate. The proven zirconium resources in the world are about 19 million tons. Zirconium oxide is usually produced by purifying zirconium ore. Under normal pressure, pure ZrO2 has three crystal states: monoclinic zirconia (m-ZrO2), tetragonal zirconia (t-ZrO2) and cubic zirconia (c-ZrO2),
forming
The molding of zirconia ceramics includes dry pressing molding, isostatic pressing molding, injection molding, hot die casting molding, casting molding, injection molding, plastic extrusion molding, colloidal solidification molding and so on. Among them, the most widely used are injection molding and dry compression molding.
sintering
The sintering methods that can be used for zirconia ceramics are generally as follows: (1) pressureless sintering, (2) hot press sintering and reaction hot press sintering, (3) hot isostatic pressing sintering (HIP), (4) microwave sintering, (5) ultra-high pressure sintering, (5) discharge plasma sintering (SPS), ⑺In-situ pressure molding and sintering, etc. It is often based on pressureless sintering.
05 Calcium oxide ceramics
Product features and advantages:
Calcium oxide ceramics (calcia ceramics) refer to ceramics with calcium oxide as the main component.
Properties: Calcium oxide has a NaCl-type crystal structure with a density of 3.08~3.40g/cm3, a melting point of 2570°C, thermodynamic stability, can be used at high temperatures (2000°C), and has a small reaction with highly active metal melts. There is little pollution of oxygen or impurity elements. The product has good resistance to molten metal erosion and molten calcium phosphate. It can be formed by dry pressing or grouting.
Ceramic sintering
is the general term for the compaction process and phenomenon of green body at high temperature.
As the temperature rises, the ceramic green body has powder particles with a larger specific surface and higher surface energy, trying to change to the direction of reducing the surface energy, continuous material migration, the grain boundary moves with it, the pores are gradually eliminated, and shrinkage occurs. Make the body into a dense porcelain body with a certain strength.
The driving force for sintering is surface energy. Sintering can be divided into sintering with liquid phase participation and pure solid phase sintering. The sintering process is very important for ceramic production. In order to reduce the sintering temperature and expand the firing range, some additives are usually added as fluxes to form a small amount of liquid phase to promote sintering. Such as adding a small amount of silica to promote the sintering of barium titanate ceramics; and adding a small amount of magnesium oxide, calcium oxide, and silica to promote the sintering of alumina ceramics.
05 Boron carbide ceramics
Preparation of
B4C powder The preparation method of B4C powder can refer to the preparation method of SiC powder. For the preparation method of reducing boric anhydride with carbon, the reaction formula is as follows:
2B2O3+ 7C⇋B4C + 6CO
This method is to indirectly heat the ingredients or directly pass the current through the ingredients in the resistance furnace and electric arc furnace. When the temperature reaches 2200℃, B4C decomposes into It is rich in carbon and boron, and boron will volatilize at high temperature. The B4C produced in the electric arc furnace contains a large amount of free graphite with a content of 20% to 30%. The B4C prepared in the resistance furnace contains a small amount of free carbon, but contains free boron, with a content of 1% to 2%.
In the presence of carbon, the boron anhydride is reduced by the magnesium heating method, which can produce very fine boron carbide powder, and the magnesium oxide is washed with acid. In this boron carbide, magnesium and free boron may be the main impurities. Due to the low temperature in the process, the free boron content is slightly more than the boron carbide prepared by reducing boron anhydride with carbon in the resistance furnace.
Forming and firing
Boron carbide ceramics can be formed by various methods. In order to obtain dense B4C, it is generally made by hot pressing sintering method. The hot-pressed sintered B4C can reach 98% of the theoretical density. It is prepared in a vacuum hot-pressing furnace or a common hot-pressing furnace. The hot-pressing temperature is 2100°C, the pressure is 80~100MPa, the temperature is kept for several minutes, and the pressure needs to be maintained when the temperature is reduced. . Due to the poor thermal shock resistance of B4C, it is necessary to cool down slowly. The hot pressing temperature should not be too high. B2C-C eutectic liquid phase will appear at 2150℃, but if the temperature is too low, the product density will be low. Using B4C ultrafine powder raw materials, boron carbide ceramic products with high density and hardness can be obtained.