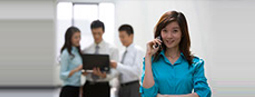
Suzhou Kaifa New Material Technology Co., Ltd.
Email:heqing@szkfxc.com
Email:sales@szbknm.com
Email:bkxc.bonnie@gmail.com
The secret of alumina ceramic "wear resistance"
"Friction" is a fairly common phenomenon that accompanies human activities all the time, such as friction for walking, friction for running a car, and friction for running a train. The physical phenomenon caused by this relative motion seems to be very friendly to humans, but in fact it often shows a hideous side.
For example, in industry, the "friction" between two objects is often harmful, causing wear on the contact surfaces of the objects, and severe wear can even cause the normal working motion mechanism to fail. In order to deal with this industrial enemy, people often use advanced ceramic materials with excellent wear resistance as a substitute for ordinary metals or plastics, or cover the surface of vulnerable workpieces with wear-resistant ceramics to improve their durability.
Compared with ordinary metals or plastics, wear-resistant ceramics have the following advantages: high hardness, high strength, good wear resistance, more than 100 times more than manganese steel, high chromium steel, high temperature resistance, acid and alkali corrosion resistance, light weight, only Half of the steel can greatly reduce the load of the equipment. Among them, alumina ceramics are quite suitable for industrial applications due to their very affordable prices, and have become one of the most commonly used wear-resistant materials in this field. Wild and unrestrained” occasions can be seen everywhere.
Since the friction and wear properties of ceramic materials are very important to their good service, in order to "control" the friction of alumina ceramics, it is necessary to understand and study the relationship between it and friction.
The relationship between alumina ceramics and friction
Evans has systematically studied the factors affecting the wear rate of ceramic materials and found that the hardness and fracture toughness of ceramic materials are the key factors affecting the wear rate, and the wear rate of ceramic materials with high hardness and fracture toughness is lower. In order to improve the hardness and fracture toughness of ceramic materials, scholars from various countries have carried out a lot of research work, which can be analyzed in the following aspects:
1. Ceramic grain size
Alumina ceramic materials are divided into single-phase ceramics and multi-phase ceramics (that is, adding a second phase to the matrix). The effect of grain size of two phases) on the tribological properties of ceramics.
For example, Roy et al. studied the friction and wear properties of submicron and micron single-phase alumina ceramics in biological environments, and found that the wear rate of submicron ceramics in the bovine serum albumin environment was much lower than that of micron ceramics, and the wear rate of submicron ceramics was much lower than that of micron ceramics. Grain pullout and grain boundary microcracks are significantly less than in coarse-grained alumina ceramics. Sedlacek et al. studied the effect of different alumina matrix grain sizes on wear performance, where the matrix alumina grain size varied from 0.8 to 4 μm, while the second phase SiC was nano-sized. Studies have shown that when the alumina matrix is in the sub-micron size, the wear resistance is better than that of the nanocomposite ceramics with micron grain size; when the matrix grains are in the sub-micron scale, there is no obvious relationship between wear resistance and fracture toughness, while the matrix is in The wear rate of micron-scale alumina multiphase ceramics decreases with increasing hardness.
Obviously, it can be seen from the above examples that grain refinement can effectively help improve the uniformity of the material structure, including improving the density of the material and reducing the defects of the material.
2. Second phase material
In the field of research on the tribological properties of alumina multiphase ceramics, the compounding of components, that is, the formation of composite materials by adding various second phases, particles (or whiskers) is also the main way to improve the tribological (or cutting) properties of alumina ceramics . According to different influence mechanisms, it can be divided into several types, such as the second-phase self-lubricating mechanism, the second-phase grain boundary enhancement, and the second-phase tribochemical reaction mechanism.
①Second-phase self-lubricating mechanism
The introduction of graphite, CaF2, PbWO4, MoS2, BN, soft metals and other second-phase solid lubricants into the Al2O3 ceramic matrix can effectively reduce the friction coefficient of the material, thereby improving the tribological properties of the material. Deng Jianxin et al. introduced 10% CaF2 solid lubricant into the Al2O3/TiC composite ceramic matrix. Through cutting and friction experiments, it was found that CaF2 was extruded and smeared on the friction surface to form a self-lubricating film, and the self-lubricating film can effectively prevent the material from interacting with the material. The adhesion between the friction pairs reduces the friction factor and plays a self-lubricating role.
② Grain boundary enhancement of the second phase
The second phase (mainly particles and whiskers) is introduced into the alumina ceramic matrix, and the difference in thermal expansion coefficient between the dispersed particles and the matrix material is used to generate residual stress during the material preparation and cooling process to achieve the effect of grain boundary enhancement. When expanding along the grain boundary, it is necessary to overcome not only the inherent grain boundary energy of the matrix material, but also the additional energy brought by the residual compressive stress, thereby increasing the crack propagation resistance; on the other hand, since the thermal expansion coefficient of the second phase particles is less than The thermal expansion coefficient of the matrix, the volume effect will occur during the cooling process of the material, and micro-cracks will be generated around the second-phase particles, which will induce crack deflection and consume more energy for crack expansion; in addition, generally, the second-phase particles are approximately round. The spherical shape makes the crack tip passivated, thereby reducing stress concentration and preventing crack propagation, thereby improving the tribological properties of the material.
③Second-phase tribochemical reaction mechanism
The second-phase tribochemical reaction mechanism means that the second phase doped in the Al2O3 matrix reacts chemically with the gas (mainly oxygen) in the air or with the counter-grinding pair material when rubbing against the counter-grinding pair material to produce a lubricating film. Reduce the friction factor of the material, thereby improving the tribological properties of the material.
Deng Jianxin et al. introduced TiB2 particles into the Al2O3 ceramic matrix to prepare an Al2O3/TiB2 composite ceramic tool. When the tool was tested with 45# hardened steel, it was found that when the cutting speed was greater than 120m/min, that is, when the cutting temperature was greater than 800 °C, Al2O3 The TiB2 in the /TiB2 composite ceramic tool chemically reacts with oxygen to generate TiO2 and B2O3. Since the elastic modulus and hardness of TiO2 are much lower than those of the matrix material, the shear strength is reduced, and the friction coefficient of the material is reduced. It reduces the adhesive wear of the tool and improves the wear resistance of the tool.
3. Tribological mechanism
In different application situations, the tribological mechanism of alumina ceramics is actually different, so different strengthening methods should be combined to find the right remedy. At present, researchers have carried out extensive research on this aspect, and have obtained some regular understandings:
Deng Jianxin et al. studied the tribological mechanism of two high-temperature self-lubricating ceramic tool materials, Al2O3/TiB2 and Al2O3/TiC/CaF2. The study found that the wear mechanism of Al2O3/TiB2 ceramic tools is adhesive wear and abrasive wear during low-speed dry cutting; while in high-speed dry cutting, the tool wear mechanism is oxidative wear, and the surface of the tool is generated by a reaction film through tribochemical reactions. It plays the role of solid lubrication and improves the wear resistance of the tool. With the increase of TiB2 content and cutting speed, the anti-friction and anti-wear effect of the reaction film is enhanced.
Yao Shuqing et al. studied the tribological properties and mechanisms of three Al2O3-based ceramic tool materials added with different second phases. The research shows that the tribological properties of Al2O3-based ceramic tool materials are related to the types of additives, and their anti-wear properties are from large to small. The order is Al2O3/SiCw, Al2O3/Ti(C,N), Al2O3/TiC; and the tribological properties of the material are related to its hardness (H), elastic modulus (E) and fracture toughness (KIC), and the wear rate W increases with E/H increases and decreases with the increase of KIC; the wear mechanism of Al2O3/TiC ceramic tool materials is mainly adhesive wear, and the wear mechanism of Al2O3/Ti(C, N) and Al2O3/SiCw ceramic tool materials is mainly abrasive wear. Grain wear is the main factor.
Summarize
The friction and wear performance of materials is a comprehensive performance, which is affected by many factors. However, various studies have shown that grain refinement and component recombination can indeed effectively improve the strength and fracture toughness of alumina ceramic materials, thereby improving their tribological properties. If the research in this area can continue to improve, it will be able to effectively promote the further application of alumina ceramic materials in various fields.
source:
Tribological research progress of Al2O3 ceramic materials, Huang Weijiu, Wu Guisen.